a change in safety culture requires osha quizlet
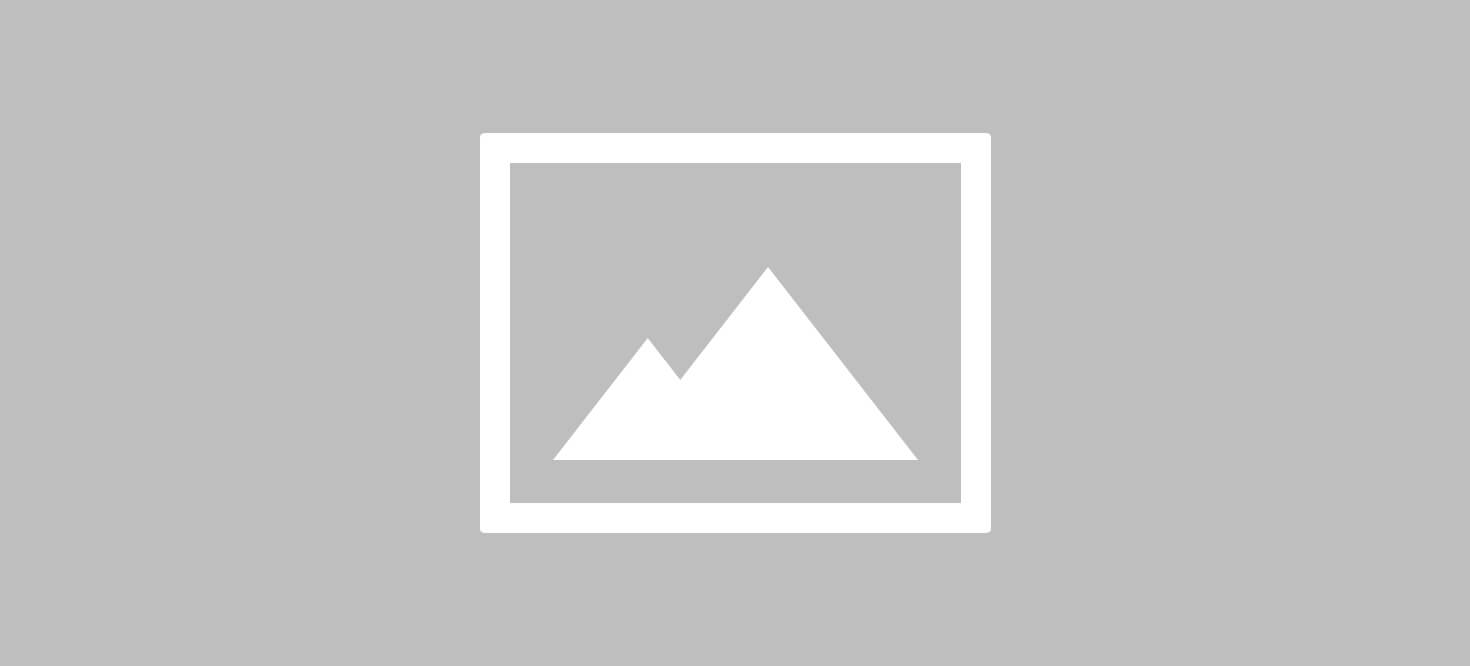
As soon as the incumbent CEO signs the health and safety policy, it should be communicated to each employee and carried out with no exceptions. Occupational Safety & Health Administration, Occupational Safety and Health Administration, Outreach Training Program (10- and 30-hour Cards), OSHA Training Institute Education Centers, Safety and Health Management Systems in Hospitals, OSHA's Voluntary Protection Program (VPP), The Lucian Leape Institute at National Patient Safety Foundation, Improving Patient and Worker Safety: Opportunities for Synergy, Collaboration and Innovation, NORA Healthcare and Social Assistance Sector Council, Severe Storm and Flood Recovery Assistance. Illegal/Unlawful -Emoloyers must maintain an OSHA-300 log, and make it avilable to workers -Employers must post the annual summary -Emoloyers must report fatalities and any hospitalization to OSHA Section 11 (c) Prohibits employers from discriminating against worker for exercising their safety and health rights What does OSHA require employers to post for 3 days The management team developed an intervention to break the entrenched culture of not stopping to ask for help in potentially risky situations. Employers are also prohibited to discriminate against workers who have filed complaints against employers. Based on the positive experience of employers with existing systems, OSHA believes that safety and health management systems provide the foundation for breakthrough changes in the way employers identify and control hazards, leading to significantly improved overall workplace health and safety environments; improved patient safety; and fewer worker injuries, illnesses and fatalities. After initially focusing on common occupational health and safety hazards, OSHA started working on a more holistic approach to workplace safety and health beginning in the 1980s by starting education, training, and consultation programs outside of standard enforcement. 2Siegel JD, Rhinehart E, Jackson M, Chiarello L, and the Healthcare Infection Control Practices Advisory Committee, 2007 Guideline for Isolation Precautions: Preventing Transmission of Infectious Agents in Healthcare Settings. To help improve the safety of the workplace we have listed below the OSHA standard checklist for the general industry. Even so, an organization can improve upon safety only when leaders are visibly committed to change and when they enable staff to openly share safety information. Once submitted, OSHA will then indicate any penalties and will require abatement plans and progress reports to ensure effective correction of cited violation/s. Notify all affected employees that a lockout/tagout is about to begin. For example, an industrial company recently used advanced analytics to pull together data sources outside its HSE system, including data on production, human resources, and weather, to identify the primary factors that contribute to employee safety. Stopping short in this way allows management to feel there is little they could have done to prevent the incident, even though it is their job to ensure people are empowered to follow the rules. For non-compliance or partial compliance after an inspection, employers are required to post OSHA citations, until the violation has been corrected, near the area where the violation has been identified. An operator at a steel plant was adding alloys to a molten metal ladle. what challenges if any have people encountered with sustainability of Leadership walkRounds? EHS managers should implement a real-time incident reporting through mobile-ready OSHA 300 forms to identify leading indicators to safe performance. Providing training and being clear about their role in these safety programs ensure that they are well prepared in the performance of their duties. Environmental, health, and safety managers should update these guidelines when applicable OSHA standards change and integrate it with lessons learned from past incidents, new insights from recent training sessions, and more efficient SOPs. Roughly 80 percent of the factors that were found to be statistically significant were neither measured nor accounted for in the companys original investigation methodology. The Recommended Practices are designed to be used in a wide variety of small and medium-sized business settings. There are five essential components to any type of successful organizational change. The lack of a safety culture as a contributing factor to HCW noncompliance with recommended infection control guidance is not a newly recognized problem. More changes will be made to workplace health rules no later than mid-April following public health's announcement. Examples of energy isolating devices are: Energy isolating devices DO NOT INCLUDE push buttons, selector switches, and other control circuit type devices. The difference between lock out and tag out is the device used. If not, do not attempt removal and notify the safety supervisor. The OSHA standards for Construction and General Industry are found in: Parts 1926 and 1910 OSHA standards fall into four categories (or Parts): General Industry, Construction, Maritime, and Agriculture True OSHA standards appear in the Code of Federal Regulation (CFR) True (letter may vary; Individuals with great communication skills, Individuals work to gain trust and respect of others, and The overall sharing of vision and passion) The knowledge that the industrial accident situation is deteriorating, rather than improving, underscores the need for action now. US Senator Harrison A. Williams Jr. On December 29, 1970, then US President Richard Nixon signed the Occupational Safety and Health Act of 1970 which spawned three different agencies, each focused on a different aspect of health and safety in the workplace: Officially established on April 28, 1971, OSHA became the first nationwide regulating body in the United States tasked with setting and enforcing workplace safety standards for the benefit of private-sector and government workers. j. a young woman of the 1920s who adopted a certain style of dress and behavior Minor injuries that can be remedied with first aid do not need to be recorded. The whole program of our disaster training is anchored on safety so seeing to it that no one gets harmed during the activities ensures that the efficiency of the team is sustained. A simple, easy-to-use tool that front-line staff can use to share information about potential safety problems and concerns on a daily basis, to promote safety consciousness and learning. Facilitate peer-to-peer observations, provide informal feedback, and engage in follow-up discussions to further support safe behavior among employees. All rights reserved. Therefore, efforts to reduce the rate of medical error must be linked with efforts to prevent work-related injury and illness if they are to be successful. OSHAs compliance safety and health officers visit workplaces and perform on-site inspections to identify and point out potential safety hazards to employers and employees. a. bIssuance of the bonds on July 31, 2012. Employers must provide the appropriate personal protective equipment (PPE) to each employee where necessary. OSHA's Hazard Communication Standard (HCS) requires the development and dissemination of such information: Chemical manufacturers and importers are required to evaluate the hazards of the chemicals they produce or import, and prepare labels and safety data sheets to convey the hazard information to their downstream customers; All employers with . Reason*: The employer must ensure that first aid services and medical provisions are available for all employees. Marcus Garvey Washington, DC: The National Academies Press. Select One The following information is primarily based on the OSHA lockout tagout standard: An energy isolating device is a mechanical device that physically prevents the transmission or release of hazardous energy. Employers must ensure that the following spaces are inspected and tested by a qualified person to determine the atmospheres oxygen content before employees are allowed entry: Employers must ensure that all rooms determined to be oxygen-deficient or oxygen-enriched are labeled Not Safe for Workers., Employers must ensure that the oxygen content for all rooms and spaces are within the range of 19.5 percent and 22.0 percent. In providing effective safety education and training, specific action items must be observed: OSHA standards training is a crucial part of safety and health programs because it is designed to aid workers in protecting themselves from injuries and illnesses. Self-employed workers and workers protected by other federal agencies such as the Mine Safety and Health Administration are not covered by OSHA. Companies looking to improve workplace safety have a number of methods at their disposal. 1/1/2017 7:36:15 AM, by Tracey Burns must adopt safety principles and demonstrate them through their behaviours At an Asian chemicals manufacturer, hand injuries accounted for about 50 percent of all serious injuries. To help you and your team get started, download and use the following OSHA checklists for free: Jona Tarlengco is a content writer and researcher for SafetyCulture since 2018. Journalize the following transactions: **10. fundamentalism, CAL/OSHA 10/30 Construction - Updated 04/2022, (letter may vary; Comply with all OSHA standards and rules, Comply with all company established health and safety requirements, and Be held responsible for complying to established requirements). 1/31/2018 2:57:10 AM. This site is best viewed with Internet Explorer version 8 or greater. Employers must provide fall protection such as guardrails, safety nets, and safety harnesses to employees working at a height of six feet or more. Their message about safety must be consistent and sustained, as it takes a long time for culture to change. Forward-Looking Accountability. At the same time, you should also find a way to confirm that LOTO procedures are being followed and respond to urgent issues quickly. 8. flapper For example, a metals producer, having adopted a zero goal, set stretch but achievable targets for injury reduction and expanded the set of HSE metrics to include positive, leading indicators such as the number and quality of field interactions. What measures were effective in removing these challenges? You can also offer incentives for positive behavior as encouragement. 10/27/2016 5:12:05 AM, by Andrew McCullough This can include inspecting the various equipment and machines to which the OSHA lockout tagout standard applies and the lockout tagout devices used in the facility. Selecting a culture of safety requires both leadership and employee commitment. What to Do if An Employee is Not Available to Remove the Lock. For this reason, one of the most important duties of the employer is to eliminate preventable workplace hazards. Define goal congruence, and explain why it is important to an organization's success. What rights and responsibilities did Rome extend to conquered peoples? Start fresh with self honesty. This section talks about some of the most prominent employer responsibilities regarding the safety and health of employees in the maritime industry as mandated by OSHAs standards: Maritime checklists help employers to keep their employees safe. D. All of the above, (letter may vary; Providing appropriate feedback such as coaching, ASKING for feedback from employees and coworkers, Providing timely praise and recognition when appropriate, and setting reasonable expectations for safe performance) In our experience, two actions can help reverse this mind-set. Below are OSHAs designated color recommendations when informing workers of potential hazards: OSHA has also established safety codes that should be used when physical hazards are present in the facility: OSHA borrows from the American National Standards Institutes (ANSI) color-coding scheme to provide workers instructions aimed at maximizing safety. If such measures fail, employers must ensure that employees have access to PPEs which protect them from excessive noise exposure and harmful sound levels. c. Accrual of interest on December 31, 2012. The Centers for Disease Control and Prevention's Healthcare Infection Control Practices Advisory Committee has noted that "several hospital-based studies have linked measures of safety culture with both employee adherence to safe practices and reduced exposures to blood and body fluids. A Safety and Environmental Management System (SEMS) is a performance-based approach to integrating and managing offshore operations. While primary collaboration is with the head of the facility or your employer, you should also obtain clarification from employees regarding their concerns, especially about equipment safety. (pick two) a) Recognition and avoidance of unsafe conditions b) How to carry out their duties The Recommended Practices present a step-by-step approach to implementing a safety and health program, built around seven core elements that make up a successful program. Develop a Culture of Safety. With SafetyCulture, safety officers can: complete JSA inspections anytime, anywhere even if they are offline; This white paper provides information on the development and methodology of the IHI Global Trigger Tool, enabling the ability to accurately identify adverse events and measure the rate of adverse events over time. Changing the safety culture of an organization can be difficult and is not a simple task. This learned tolerance to risk has to do with the pervasive belief that some risks cant be mitigated. Zora Neale Hurston Failure to comply with OSHAs standards can lead to hefty fines, legal consequences, and a tarnished reputation. [They are:], (letter may vary; Allowed, Encouraged, and Ignored). The National Occupational Research Agenda (NORA) Healthcare and Social Assistance Council brings together individuals and organizations to share information, form partnerships, and promote adoption and dissemination of solutions that work. Her 5-year experience in one of the worlds leading business news organisations helps enrich the quality of the information in her work. Employers will find that implementing these recommended practices also brings other benefits. Even those managers committed to change often have low expectations about the pace of improvement, while the uncommitted engage in passive resistancethey wait things out. What is the Difference Between Lock Out and Tag Out? Check your browser compatibility mode if you are using Internet Explorer version 8 or greater. Worker participation makes an important contribution to an employer's bottom line. the set of shared safety attitudes, beliefs, and practices that shape employees' safety behavior, Not the direct cause but still adds to the cause, The action or situation that initiates a problem, Edge that does not have an existing guard rail, The unprotected side and edge of a floor, roof, or form work for a floor or other walking/working surface (such as deck) which changes location as additional floor, roof, decking or form work sections are placed, formed or constructed, Act that requires employers subject to OSHA to provide employees with a safe and healthy work environment, A person who is capable of identifying existing and predictable hazards in the surroundings or working conditions which are unsanitary, hazardous, or dangerous to employees, and who has authorization to take prompt corrective measures to eliminate them, U.S. law authorizing the federal government to enforce safety and health standards for all places of employment engaging in interstate commerce, Protects workers who report violations of OSHA's laws and regulations to OSHA so you cannot be fired, A person who, by possession of a recognized degree, certificate, or professional standing, or by extensive knowledge, training, and experience, has demonstrated the ability to solve or prevent problems relating to a certain subject, work, or project, any person authorized by the employer & required by work duties to be present in regulated areas, Occupational Safety and Health Administration, OSHA 30 Construction Test Answer Key FALL HAZ, OSHA 30 Construction Test Answer Key ELECTROC, osha 30 module 14 personal protective equipme, Chapter 2 Family-Centered Community-Based Care. An abatement is the correction of a violation related to safety that led to an OSHA citation. When incidents arent reported, management and workers lose the opportunity to learn from near misses and low-severity events. After a while, employees took such pride in the tokens that they started putting $5 bills in the bins so they could keep the tokens. At that time, wearing a mask in the workplace will no longer be mandatory, but . To conduct a LOTO inspection, the safety supervisor or authorized employee must do the following: LOTO inspections must be conducted at least annually or more often if necessary. By identifying these mind-sets and harnessing approaches to overcome them, companies can achieve rapid, sustained change. Several studies have found organizational factors to be the most significant predictor of safe work behaviors. / Most employees come to work to get things done and feel satisfied when they hit their targets. and health risks at work. Employees must know their responsibilities and work alongside their employers to implement a culture of safety for the benefit of both parties. I have a metallurgic procedure in the blue binder and a safety procedure in the gray binder. The operator, however, was using neither. Safety and health programs help businesses: Recommended Practices for Safety and Health Programs (en Espaol) One obvious way to combat this issue is for leaders to develop clear safety standards that take existing processes into account while integrating safety and productivity requirements. During the course of construction work, employers must ensure that harmful debris such as scrap lumber, protruding nails, and others are cleared from work areas, passageways, and stairs. Moving beyond mere regulatory compliance, adherence to OSHA standards protects workers from deadly safety hazards and health risks at work. A. Equipment and machinery are de-energized during servicing and maintenance, Equipment control valve handles are provided with a means for locking out, Stored energy is released before equipment is locked out for repairs, Employees have individually-keyed personal safety locks, ISO 45001:2018 Occupational Health & Safety Management, Getting started with SafetyCulture Platform. Construction, agriculture, and maritime operations, Installations under the exclusive control of electric utilities, Work on cord-and-plug-connected electrical equipment in which equipment is unplugged and the authorized employee has exclusive control of the plug, , maintenance, minor tool changes or adjustments, and hot tap operations wherein employees are sufficiently protected by other safeguarding measures, From October 2020 to September 2021, the OSHA lockout tagout standard has had, 1,440 citations amounting to a total penalty of $9,369,143, . Here are 5 benefits of complying with OSHA requirements: Senior management should create a health and safety policy with clear objectives, indicating the basic health and safety philosophy of the organization. Federal Government. When workers are encouraged to offer their ideas and they see their contributions being taken seriously, they tend to be more satisfied and more productive. Eliminate manual tasks and streamline your operations. C. D. Rom has just given an insurance company $35,000\$35,000$35,000. In many organizations, these investigations end after leadership establishes that the employee made the wrong decision. Failure to shutdown. Knowing the programs structure, plans, and procedures, ensures that everyone can develop, implement, and improve the program. By approaching safety change strategically it is possible to create a climate that is conducive to improving a safety culture. I find the tips on developing a culture of safety very useful for our training sessions in disaster work. A month after OSHA became official, they released their first standards for safety and health in the workplace, including guidelines on how to protect workers from excessive noise, cotton dust, and asbestos, as well as acceptable exposure limits for more than 400 toxic substances. \text { Beginning inventory } & \$ 58,000 & \$ 100,000 \\ They also need to keep an updated record of work-related injuries and illnesses if they have 10 or more employees. Essentially, OSHA operates with two main functionsas a safety enforcer and as a safety consultant: OSHAs most prominent function is to ensure that employers and employees all over the United States comply with their safety standards. The first step to improving safety culture is to assess the current status of an organization or hospital, generally accomplished via survey. Cited primarily as the national authority in workplace safety, OSHA has multiple functions that lead to the achievement of its mission: a safe working environment for all workers. Inaction in the face of safety problems is taboo, and eventually the pressure comes from all directions from peers as well as leaders. I think having a reporting culture is also essential to improving safety in any organization. Employers must ensure that each tractor used by employees for work has a working seatbelt sufficiently tightened to keep the worker confined in the safe area within the operators station. read and follow all safety materials provided by employers, including safety information posters around the workplace; follow safe work practices as explained and demonstrated in safety training; be vigilant and pay attention to safety process updates from their employer and OSHA; report to work in a fit and stable condition and avoid work if under the influence of alcohol and other recreational drugs that may affect their cognitive functions; report identified occupational hazards and/or potential hazards to their employer for quick resolution; cooperate with OSHA compliance officers during workplace inspections; and, exercise the rights provided by OSHA responsibly. Upon joining field teams, new employees learn both from peers and supervisors the difference between a true injury and a bruise: the former should be reported and the latter should not. by Clarence Bien Nebres Despite the value to employers and workers in terms of injuries prevented and dollars saved, many healthcare institutions have not yet adopted safety and health management systems that unite patient and worker safety. One of the things on your checklist for moving to a new province in Canada, or Manitoba specifically, should be the agricultural prospects of the area; especially if you plan on making a living out of it. In your last, club newsletter you invited members to send in their original mysteries, for possible publication I have been writing stories for several years but Ive never submitted anything for publication Im enclosing a copy of my story Broken Glasses The storys setting is Exeter England I grew up there, so the setting is depicted accurately! NIOSH works in tandem with OSHA to provide new information that will positively influence and improve OSHA standards. One chemical producer sold off a factory that ranked lowest in safety, productivity, and financial performance because it believed that the plants culture was irreparable. The average monthly rent for a one-bedroom apartment . Without the proper training and knowledge, higher-ups may unwittingly put workers at risk. Such systems have been proven to help employers and society reduce the personal, financial and societal costs that injuries, illnesses and fatalities impose. Whether a permit is required depends on the declarations of the reportable disease status of the provinces . Unless management signals that safety is the priority, employees may conclude that it is acceptable to focus on productivity at the expense of safety. , a LOTO box is used when equipment has several isolation points that need to be secured (with their own energy isolating, lockout, and tagout devices) before it can be locked out. improved major safety standards covering safety management in workplaces, fall protection in construction, and enhanced electrical safety guidelines; released a new standard covering bloodborne pathogens to address biological hazards; improved PPE and Respiratory Protection Standards; developed and published lead exposure limits and standards in construction; published updated laboratory safety standards for employees who work with toxic chemicals; issued guidelines for preventing workplace violence; began actively collecting data from employers in high-risk and high-hazard industries in order to pinpoint and focus on sites with high injury and illness rates; started the Site-Specific Targeting Program which focused inspections on workplaces with the worst safety and health records; an initiative that leads to a significant decline in workplace injury and illness rates; and. d. Payment of interest on May 31, 2013. A change in perspective can have a big impact. Maintaining compliance with OSHA standards entails the commitment of the organization, its management, and all employees to prioritize health and safety. Strong and visible management leadership is perhaps the most critical element of a safety and health management system. Workers can also dispute any citations made by OSHA to the employer. Workers who are concerned for their safety or physical or psychological health in a work environment in which their safety and health is not perceived as a priority, will not be able to provide error-free care to patients.
Strictly Come Dancing 2021 Gossip,
Ocean State Job Lot Mason Jars,
What Happened To Claire On Boston Legal,
Police Incident Leeds Today,
Articles A
a change in safety culture requires osha quizlet