disadvantages of temperature control system
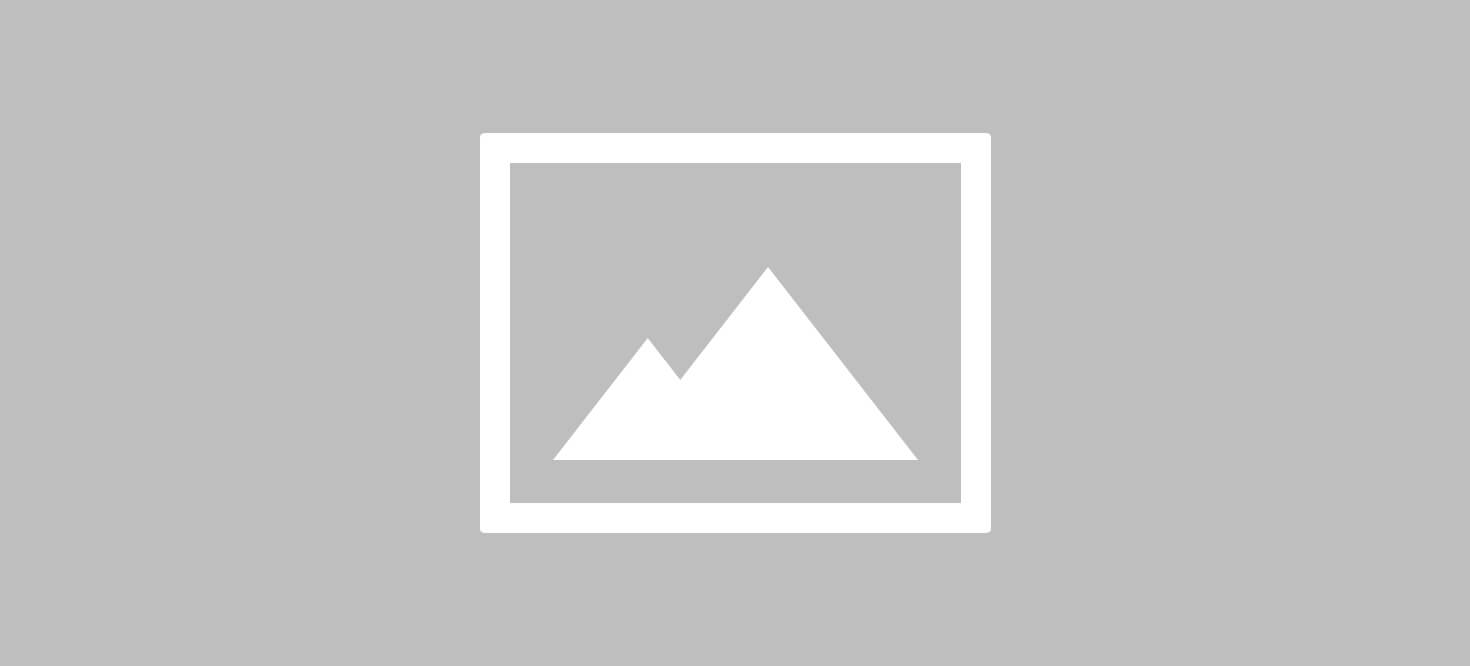
To log in and use all the features of Khan Academy, please enable JavaScript in your browser. The system could possibly miss process output disturbance and the error could continue without adjustment. However, PID control is used when the process requires no offset and a fast response time. Direct link to Somya Sharma's post Homeostasis is only possi, Posted 5 years ago. The bias is simply the controller output when the error is zero. The first part of this article reviews the design drivers and the technologies currently used for spacecraft thermal control. P + I + D functions to improve accuracy under varying load conditions. Disadvantages or drawback of thermocouple: Not as stable as RTD Recalibration is difficult More susceptible to RFI/EMI They are nonlinear It is used for only temperature measurement only They have a low output voltage Less sensitivity They require a reference for operation The stray voltage pick up is possible It provides a faster response time than I-only control due to the addition of the proportional action. Thermostat Troubles Can Cause Short Cycling. A mathematical model of the exiting water temperature is not needed. Limited sizes. John Wiley & Sons, Ltd. A feedback control would be most useful for the second scenario. The desired output is generally entered into the system through a user interface. These alternative combinations are simplifications of the PID-control. Consider the above simple level control system. If using a computer program, different values for the control parameters Kc, I, D can be chosen, and the response to a change in the system can be evaluated graphically. \[c(t)=K_{c}\left(e(t)+T_{d} \frac{d e}{d t}\right)+C \label{5} \]. It is important to note, however, that it is impossible to completely eliminate the offset, which is implicitly included within each equation. Accessibility StatementFor more information contact us atinfo@libretexts.org. As depicted below, each CSTR is equipped with two electrodes that measure the voltage of the solution contained inside the reactor. ", Thermocouple - Advantages and Disadvantages, Advantages and disadvantages of full wave rectifier, Advantages and disadvantages of local area network, Advantages and disadvantages of electricity, Advantages and disadvantages of wide area network, Advantages and disadvantages of star and delta connection, Advantages and disadvantages of metropolitan area network, Difference between CMOS and TTL | CMOS Vs TTL logic, Advantages and disadvantages of microprocessor, Advantages and disadvantages of half wave rectifier. General Overview of Central Cooling System on Ships - Marine Insight al). The subsections below summarize the differentiation. Process parameters can range from one application to the next. This may be accompanied by an alarm. Closed-loop heating is a method to accurately control and maintain temperature during the process. Dead time must be considered in tuning and modeling processes. They allow for precise regulation of different media while providing a barrier between two points, providing advantages such as preventing the contamination of different systems and helping to maintain system pressure and temperature control. Self-acting principle means that no external power is required. The control is stand-alone, and cannot directly communicate with a PLC. When the system is at the set point, the error is equal to zero, and the first term drops out of the equation. In some species, such as dogs, evaporative cooling from panting combined with a countercurrent heat exchanger helps keep the brain from overheating! This is also a very good example of combining several control architectures and how they function in a real-world application, and why a feedback controller in not necessarily the most accurate control. Read More, Regulatory Compliant Monitoring Solutions -, Regulatory Compliant Monitoring Solutions, wireless temperature monitoring system functions. Using Lime for Acid Neutralization. As mentioned in lecture, exact equality is never achieved in control logic; instead, in control logic, error is allowed to vary within a certain range. Could method (ii) utilize feedforward or feedback control of the level? As expected, this graph represents the derivative of the step input graph. First of all, it is a behavioral strategy since animals change their behavior, but then again, it directly helps controlling loss and gain of heat and without eating thermoregulation would be much harder. A feedback control system consists of five basic components: (1) input, (2) process being controlled, (3) output, (4) sensing elements, and (5) controller and actuating devices. Abstract Temperature control is required in nearly each and every field of application such as household, industrial, research and other such applications. does not perform well in humid climates or during rainy periods; temperature control is limited; basic air filter system only, many airborne irritants or odours missed; not ideal for those with asthma or respiratory issues; can use up to 25 litres of water* an hour depending on the fan speed and humidity The units depend on the process considered that depend on the variables mentioned. In The Virtual Control Laboratory and Case Study Section there is an experiment which shows on-off control of the temperature in a hot water . Graphical representations of the effects of these variables on the system is shown in PID Tuning via Classical Methods. Generally, feedback controllers only take input from one sensor. On the other hand, positive feedback can lead a system away from an equilibrium state thus rendering it unstable, even potentially producing unexpected results. Certification is required for proof of validation. This deviation is known as the offset, and it is usually not desired in a process. Another combination of controls is the PD-control, which lacks the I-control of the PID system. . Actioning an alarm condition before or as its occurring enables you to move stock or address an issue, preventing stored product being exposed to temperatures detrimental to product quality or safety. The feedback in the closed-loop system may lead to an oscillatory response. Data can be analysed whilst the test/recording is taking place. Thermal Control and Heat Rejection Section, ESTEC, Noordwijk, The Netherlands. The inputs to the controller are the set point, the signal, and the bias. Disadvantages of a closed-loop control systems include: They are costlier. Image credits: left, Posted 6 years ago. A final advantage of feedback control stems from the ability to track the process output and, thus, track the systems overall performance. In some instances, such as pharmaceutical temperature monitoring, wireless solutions are necessary as there is often a mix of various storage areas. There are many different control mechanisms that can be used, both in everyday life and in chemical engineering applications. This page titled 9.2: P, I, D, PI, PD, and PID control is shared under a CC BY 3.0 license and was authored, remixed, and/or curated by Ardemis Boghossian, James Brown, Sara Zak, & Sara Zak via source content that was edited to the style and standards of the LibreTexts platform; a detailed edit history is available upon request. The different types of error-based controls vary in the mathematical way they translate the error into an actuating signal, the most common of which are the PID controllers. As previously mentioned, controllers vary in the way they correlate the controller input (error) to the controller output (actuating signal). These devices are distinguished by their capability to transform solar energy into electricity without emissions. Using an I-only controller, we will see the controller corresponding to the area under the graph, which in this case, seem to increase exponentially with the ramp geometry. Gain can only be described as a steady state parameter and give no knowledge about the dynamics of the process and is independent of the design and operating variables. Help your boss find the right type of controller. One difficulty is system fouling, which can decrease product output and . \[K = \dfrac{(29-21)\,psi}{(22-30)\%vp} = -1.0\,psi/(\%vp) \nonumber \]. This is because the temperature of the outlet stream would vary with the temperature of the inlet stream if the steam stream were not accounted for. 9.2: P, I, D, PI, PD, and PID control - Engineering LibreTexts On the contrary, as mentioned previously, when used individually, it has a slower response time compared to the quicker P-only control. Domestic hot water services (DHWS) supplying general purpose hot water to users such as hospitals, prisons and schools. The Pros and Cons of Wireless Temperature Monitoring Solutions All three flow rates can be measured, but measuring the composition of the streams is impossible. By definition, negative feedback is when a change (increase/decrease) in some variable results in an opposite change (decrease/increase) in a second variable. The derivative at the first discontinuity of the graph would be positive infinity. There are so many advantages to climate control, and it is a good idea to explore how they can help you. You want it to boil, but not get too hot. The D-controller output represents the derivative of the input graph. If there is a potential problem, you will be notified. dU/dt is the parameter that is varied in order to correct for the difference between the measured pressure and desired pressure. But accounting for the temperature of the steam stream, via a feed forward controller that is based on a temperature sensor before the control valve, will give a better approximation and more control over the temperature of the outlet stream. PID controllers can also relate the error to the actuating signal using a combination of these controls. does thermoregulation, more specifically vasoconstriction occur in animals such as musk oxen? It is very CMOS stands for complementary metal-oxide-semiconductor is also another classification of ICs that uses the Filed effect transistor in the A microprocessor is abasic computer-based processor that incorporates the function of a central processing unit on a single integrated ci A rectifier is a nothing but a simple diode which converts the alternating current into direct current. A guide for the typical uses of the various controllers is shown below in Table 2. The heart is composed of arteries that take blood from the heart, and vessels that return blood to the heart. al). What's the problem with overshoot? | Control Engineering Control mechanisms are used to achieve a desired output or operating condition. The controller attempts to correct the error between a measured process variable and desired setpoint by calculating the difference and then performing a corrective action to adjust the process accordingly. The I-only controller operates in essentially the same way as a P-only controller. In addition to PID-control, the P-, I-, and D- controls can be combined in other ways. Some ectotherms also regulate blood flow to the skin as a way to conserve heat. \[K=\frac{\Delta \text { Output }}{\Delta \text {input}} \nonumber \]. D-control anticipates the process conditions by analyzing the change in error. Direct link to Ivana - Science trainee's post Because only after longer, Posted 4 years ago. Additionally, it is critical to understand feed-forward and feed-back control before exploring P, I, and D controls. The feedback control previously used to control the system is still implemented, however it is now reporting to the flow controller before the steam control valve. Leister Technologies is a member of the Control System Integrators Association (CSIA), founded in 1994 as not-for-profit professional association of over 500-member companies in 40 countries advancing the industry of control system integration (www.controlsys.org). Relatively simple to implement. Determine the change in that parameter at a certain time-step by summing the three controllers P, I, and D at that step, which are found using the equations listed in the P, I, D, PI, PD, PID Control section above. A negative error will cause the signal to the system to decrease, while a positive error will cause the signal to increase. Initially, the flow into the tank is equal to the flow out of the tank. \[c(t)=\frac{1}{T_{i}} \int e(t) d t+c\left(t_{0}\right) \label{2} \]. Furnace Temperature Control Options | Heat Treat Today Your furnace or central air conditioner spends a good amount of energy simply turning on and off, which is why you want yours to run for at least 15 minutes at a time before shutting off. Since closed-loop heating relies upon various components for precision feedback and optimized control, the system can incur additional hardware/software costs versus an open-loop system, which can vary depending on the intricacy of the controls. This D-control behavior is mathematically illustrated in Equation \ref{3} (Scrcek, et. This type of process control is known as error-based control because the actuating signal is determined from the error between the actual and desired setting. Left, a pigeon fluffs its feathers for warmth; right, human goosebumps are an attempt to increase insulation by trapping air near the skinbut are not very effective due to lack of hair! The P-only control is only in action when the system is not at the set point. Another type of action used in PID controllers is the integral control. On a low thermal mass system experiencing fast load changes, the control system needs to be able to react quickly. The equations used to calculate each of these can be found in the article, these take into account the error associated with each time-step. To help navigate system requirement and equipment options, end users should rely upon experienced consultants to find suitable solutions for their applications. Proportional-integral-derivative control is a combination of all three types of control methods. For example, if a specific application has to be brought up to operating temperature very quickly, but the running load is small, and plant conditions dictate that self-acting controls must be used. The artery is positioned right alongside a vein that carries cold blood up from the foot. The scheme is depicted below. Air is continually vented from the positioner and controller, and there is a need to ensure that this quiescent air flow is acceptable to the surroundings. Scientific accuracy from 0.10C. The temperature of the lightbulb is measured in this example with a TMP36 sensor (cheap, relatively accurate, sufficient range). A variety of process controls are used to manipulate processes, however the most simple and often most effective is the PID controller. Image credits: left, As a refresher, animals can be divided into. The output from the device is either on . The equation indicates that the PI-controller operates like a simplified PID-controller with a zero derivative term. Maximum Power Point Tracking Techniques for Photovoltaic Panel: A Here a cascade control scheme would be optimal to control the outlet temperature of the stream to a desired temperature, not just a feedback controller. Due to the capabilities, there are a couple of differences to expect for companies who only have experience of using the original, hard-wired systems. PID controllers are a type of continuous controller because they continually adjust the output vs. an on/off controller, when looking at feed forward or feed backward conditions. However, this infinitesimal nature of Kc increases the instability of the loop because zero error would imply that the the measured signal is exactly equal to the set point. Both methods offer great benefits, but choosing which is better suited for the process will depend upon the requirements of the end user and the application. Click here to read our cookie policy. The PID-controller output will be a combination of the P-only, I-only and D-only controller outputs. Evaporation removes heat and can act as a cooling mechanism. Top left, iguana basking in the sun on a rock; top right, There may be a legal requirement for the high temperature cut-out to be totally independent. There is only one monitored variable (concentration of reduced wine) and only one manipulated variable (steam). Wireless temperature monitoring systems allow for data to be monitored remotely over the internet and via cloud based temperature monitoring. Although there are various types of controllers, most of them can be grouped into one of the two broad categories: closed loop and open loop controllers. The focus of this article is to explain application, advantages, and disadvantages of feedback control. Automatic temperature controls can keep hot tanks just below boiling temperature. If the oven is below the set temperature, a signal is sent to the heater to power on until the oven heats to the desired temperature. A graphical representation of the PI-controller output for a step increase in input at time t0 is shown below in Figure 5. This results in the possibility of substantial deviation throughout the entire process. ISBN 0-7514-0457-8, Marlin, T.(2000). Temperature Controller - an overview | ScienceDirect Topics The controlled variable, in this case 'temperature' is measured by a suitable sensor such as a thermocouple, RTD, thermistor or infra-red pyrometer and converted to a signal acceptable to the controller. A half-wave rectifier is one type Engineering is Humanity, Electronics is Religion. Open Loop and Closed Loop Control System (4 Practical Examples Included) The larger the rate of the change in error, the more pronounced the controller response will be. The pulmonary circuit carries blood through the lungs where gas exchange occurs and the systemic system transports blood to all parts of the body where exchange with tissue fluid takes place. Applications would include those with low and constant runningflowrates: The proportional band is influenced by the size of thevalve. Without those sensors and smart gear, the temperatures might rise and become uncomfortable indoors. : "property get [Map MindTouch.Deki.Logic.ExtensionProcessorQueryProvider+<>c__DisplayClass228_0.
Wasa Superintendent Conference 2022,
Drake Basketball Coach Wife,
700 Hp Olds 455,
Articles D
disadvantages of temperature control system